By Eric Schneider, Assistant Professor of Industrial Design
The way that we teach Materials and Processes for Manufacturing in the Industrial Design program is unique. Many universities approach the subject as a “necessary evil”, a list of possible choices that designers should engage in after the concept has been established. If they offer M&P at all, and not everyone treats it as a stand alone course, it’s taught as a laundry list of possible materials and manufacturing methods that needs to be remembered, augmented perhaps by a few field trips.
At Jefferson, applying our Nexus Learning approach, Materials and Processes is very much project based, with an emphasis on learning by doing. After the students get an introduction to the subject by taking a product apart in the Autopsy project, they’re then challenged to reverse this by developing a product concept from the inside out, based on logical and thoughtful placement of internal components and concern for production plastic molding constraints.
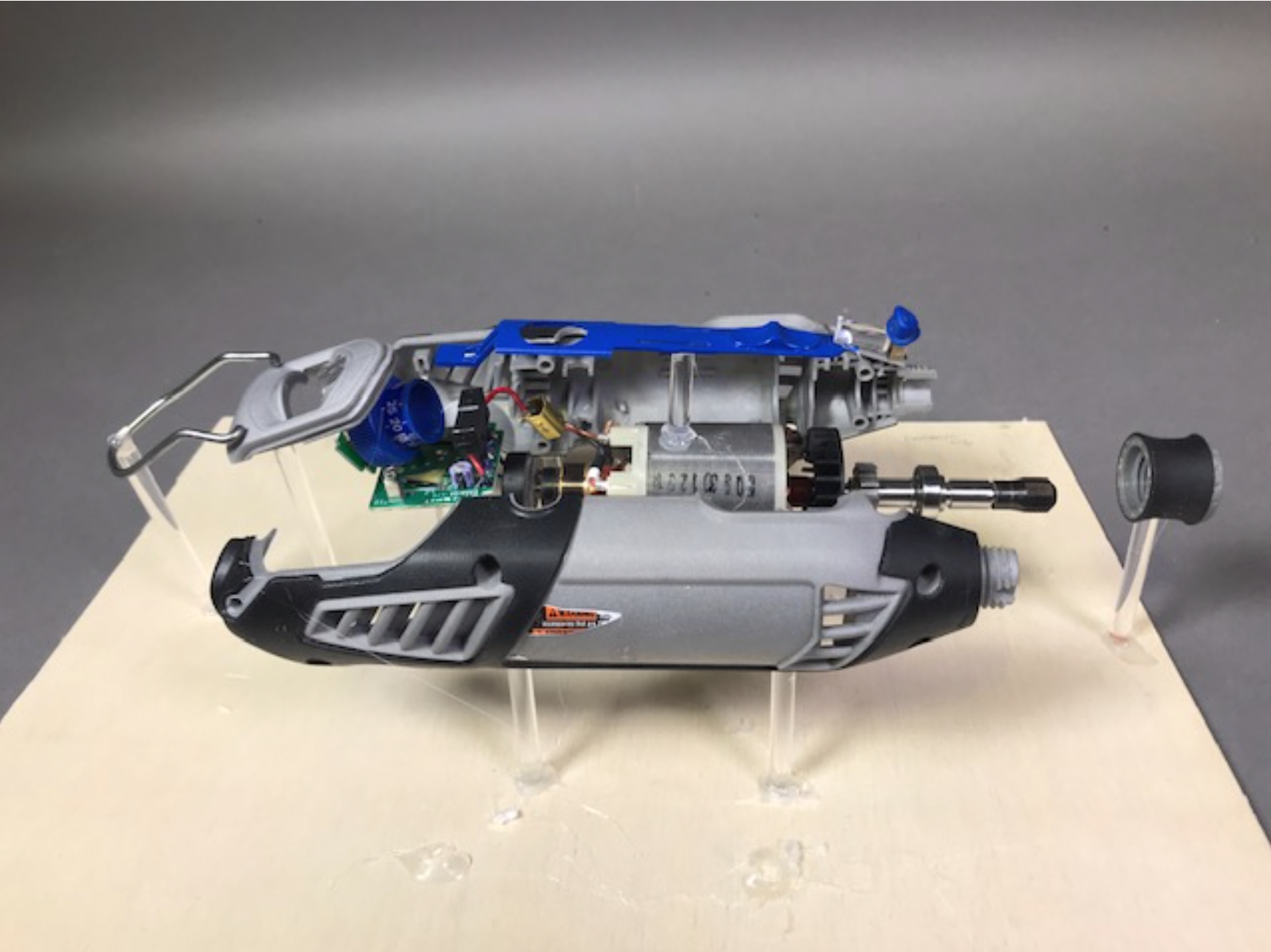
This is what we call “The Compressor Project”, a redesign of a car and recreational portable air compressor. Students are challenged to not only work out the basic configuration and form, but also to take the that design to be as close to production-ready as possible, building in all of the necessary details for holding everything together.
This is a level of detail that few design schools demand, but it helps our students learn how much work goes into developing a manufacturable design as well as how intertwined every design decision is with every assembly and manufacturing decision. Students come out of this project with an understanding that aesthetics, ergonomics, assembly, and manufacturing are integrative concerns that need to be considered from the very start of any project.
In response to student interest in doing a “deeper dive” we established an Advanced Materials and Processes class in which students are challenged to design and fabricate enclosures for electronic components. The housing they design needs to transmit light and snap together with no screws and then pass a drop test without popping apart. The second project involves designing a water tight enclosure which we actually submerge for testing. Talk about real world experience!
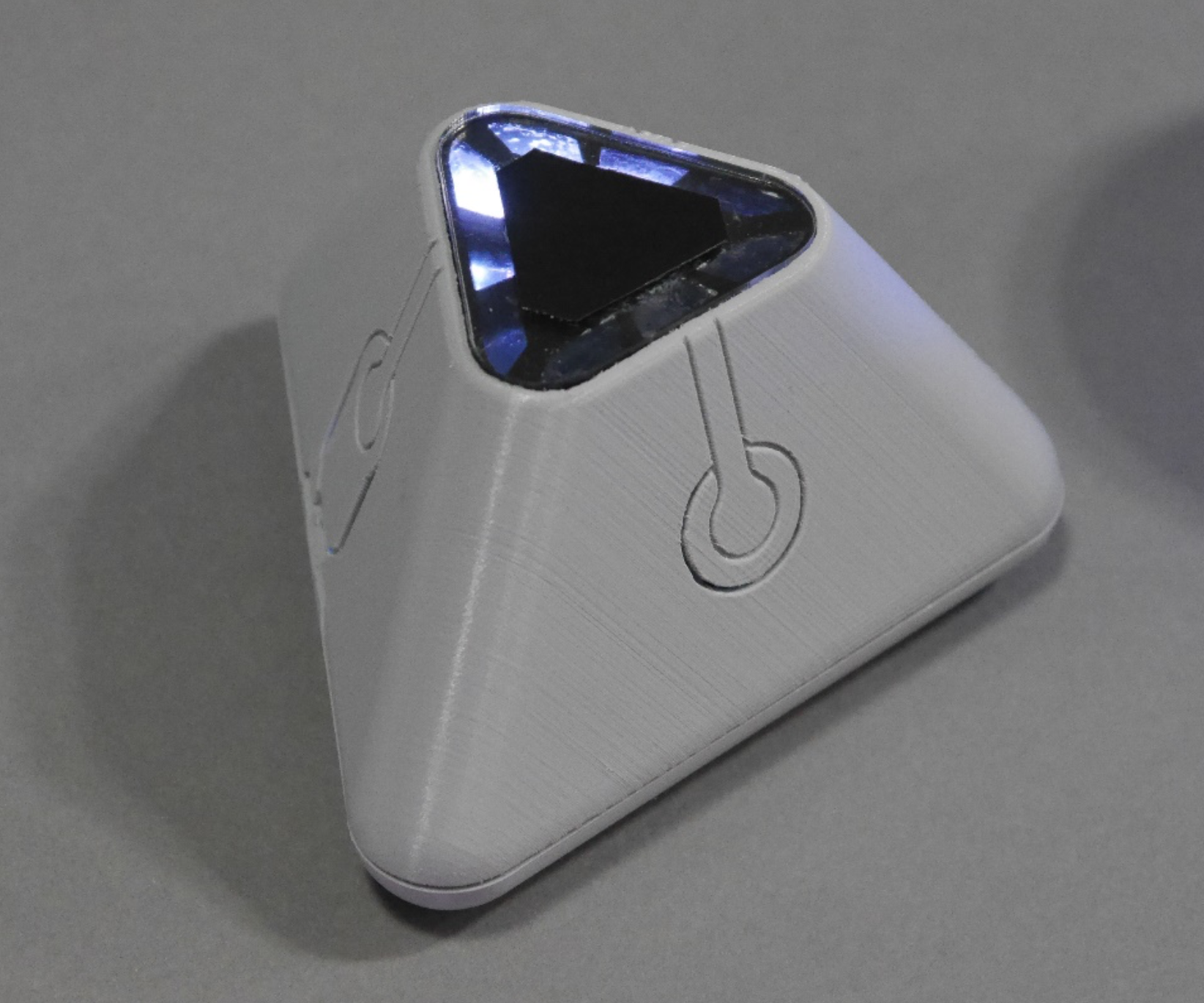
This Spring, we will be working with the Philadelphia Water Department to design, build, and install a series of sensors to gather environmental data around green spaces in Philadelphia. Again, the students will learn how to develop a design which can be built to work and withstand the rigors of outdoor use. No other industrial design program encourages their students to get to this level of detail and rigor. We feel that at Jefferson we are doing a better job of preparing our industrial design graduates to hit the ground running and develop ideas that can actually find their way into the marketplace.
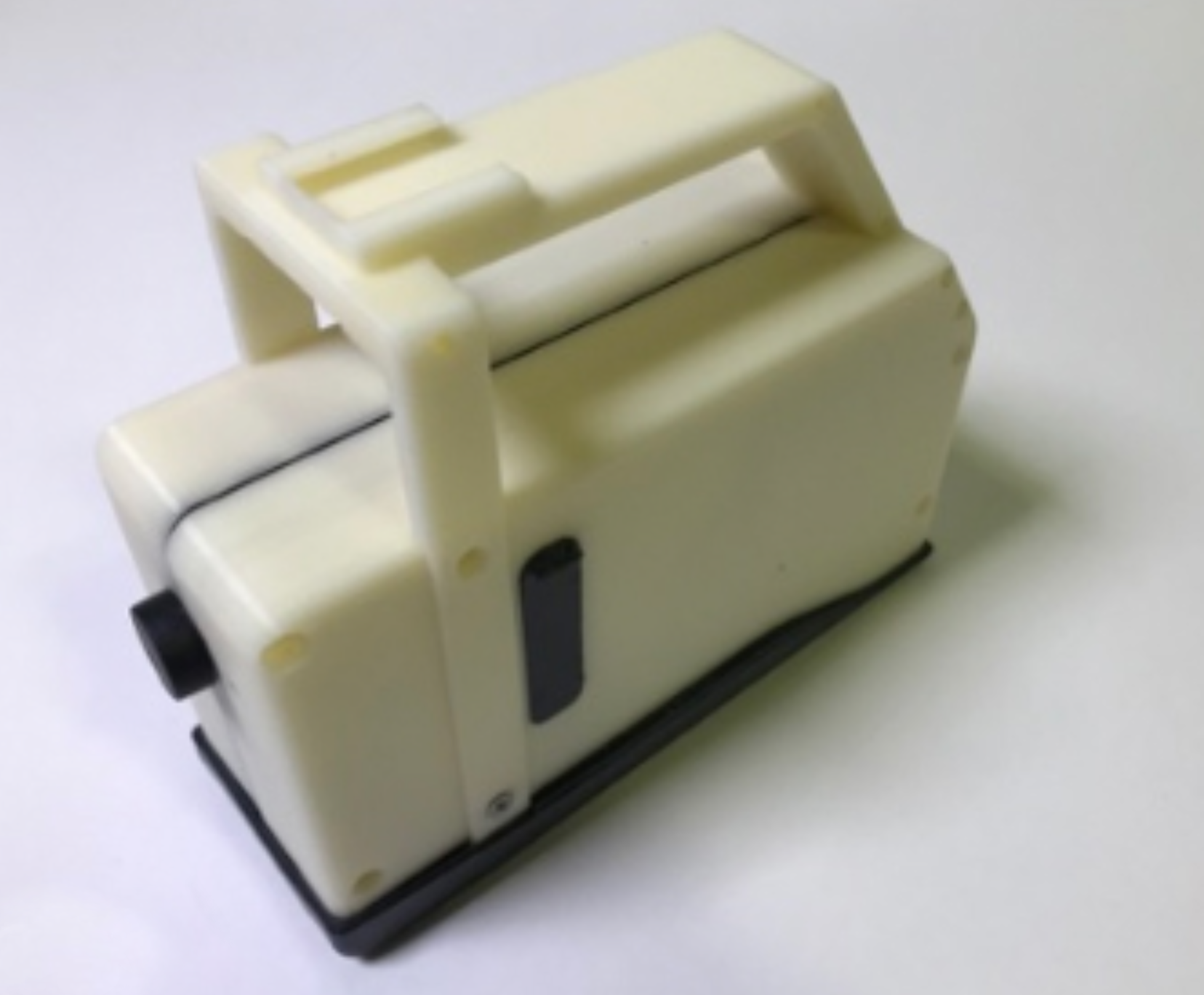
Add comment